The oil patch used to be famous for its behind-the-times mantra: “We’ve always done it this way.” But since the Shale Revolution and the increasing demand for speed, accuracy, and length in the drilling rig sector, that phrase is gone. “How can we do it better today than yesterday?” is the question for everyone.
For Scandrill’s President and COO, Paul Mosvold, and its Manager of Marketing and Contracts, Sam Hardin, balancing the speed/accuracy/length demands involves making sure no one of the three overcomes the others—especially in the speed department, which is one of the big pushes for some producers.
Paul Mosvold
“When your main goal is to get faster, faster, faster than you were yesterday, eventually you’re going to get a speeding ticket,” said Hardin. “And nobody likes a speeding ticket.”
All three must be balanced, along with safety, he noted. “We’ve got the equipment, we’ve got the people, we’ve got the rig, and we’re going to work as reasonably fast as we’re directed by our customers and as our operators can while not jeopardizing any safety and not jeopardizing our customer’s wellbore.”
Mosvold added, “You can’t just be faster, you’ve got to be more efficient. If you’re more efficient, you become faster.” He added that Scandrill does after-action reviews of each project, in concert with the client, to evaluate all systems.
Efficiency questions revolve around, “Do we need more trucks? Do we need more people, better lighting?” he said. “Now we’re talking about ways to actually improve processes, and that goes for drilling as well.”
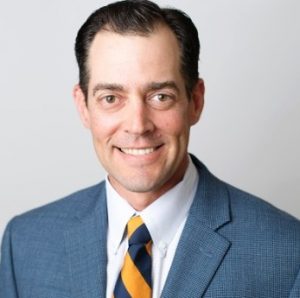
Sam Hardin
Logistics and parts supplies are a key element—making sure that all parts and supplies are onsite when or before they’re needed, so the operation does not come to a grinding halt while awaiting a warehouse delivery or a call to a supplier.
Down time is also reduced by tracking the history of each part and machine with RFID tags “on about 150 different pieces of equipment,” said Mosvold. With that they track maintenance and run hours, “so at any one given time, you know exactly where that piece of equipment is, and its life cycle.”
Knowing the life cycle informs preventive maintenance that greatly reduces failures. That, in turn, reduces down time and keeps the job moving forward, effectively creating the greater speed demanded by today’s oil field.
Rigging Up for Length
Walking rigs are certainly part of the speed equation, removing the need to tear down, transport, and reassemble a rig after every well. And with laterals now reaching 3-4 miles or more, racking capacity—the ability to tote those miles of drill pipe as the rig walks—has had to be greatly upgraded.
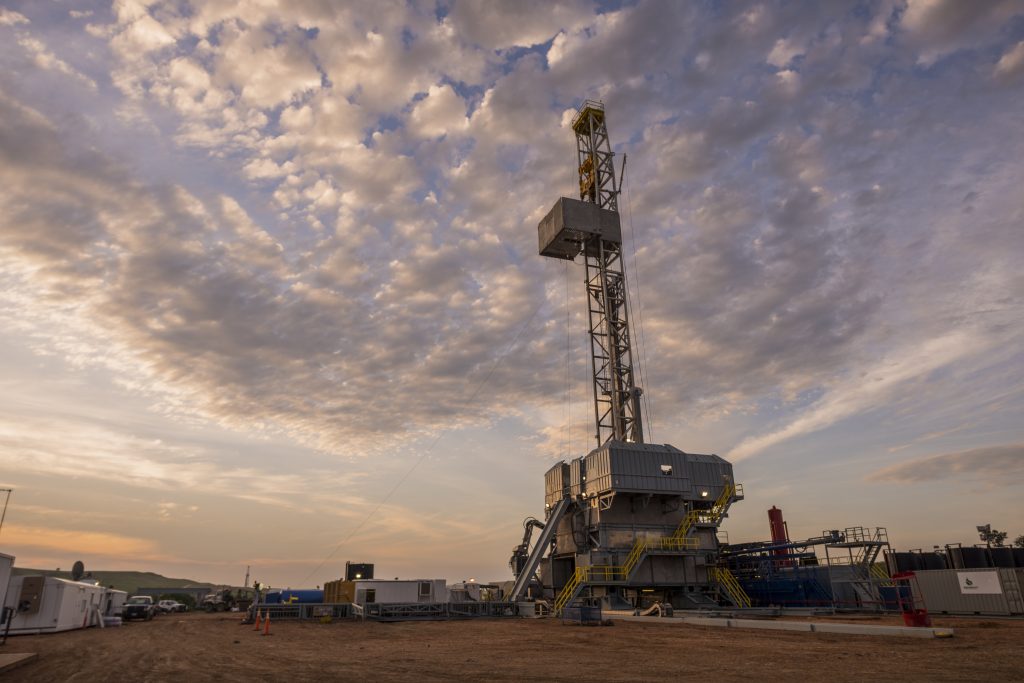
Helmerich & Payne rigs on the job.
Racking capacity of one million pounds is needed, and Mosvold said today’s rigs must be able to handle it. That massive weight creates balance issues as the rig walks—if it’s top heavy and that load shifts, a toppled rig can be a disaster.
Mosvold said the large rigs are mostly working in the Delaware Basin, East Texas’ Haynesville Shale, and deep Bossier areas. All their large rigs are deployed, but building any more rigs is not currently an option due to costs. Building a one-million-pound capacity rig is a major financial decision, as they cost about $30 million, and that cost is rising rapidly. Rig rates are not high enough to facilitate an acceptable payoff.
Mosvold explained, “If you do a five-year return on investment, rig rates would have to be at least double what they are today to make that calculation work. So [for] ourselves, no, we’re not upgrading or building any new rigs at these rates.”
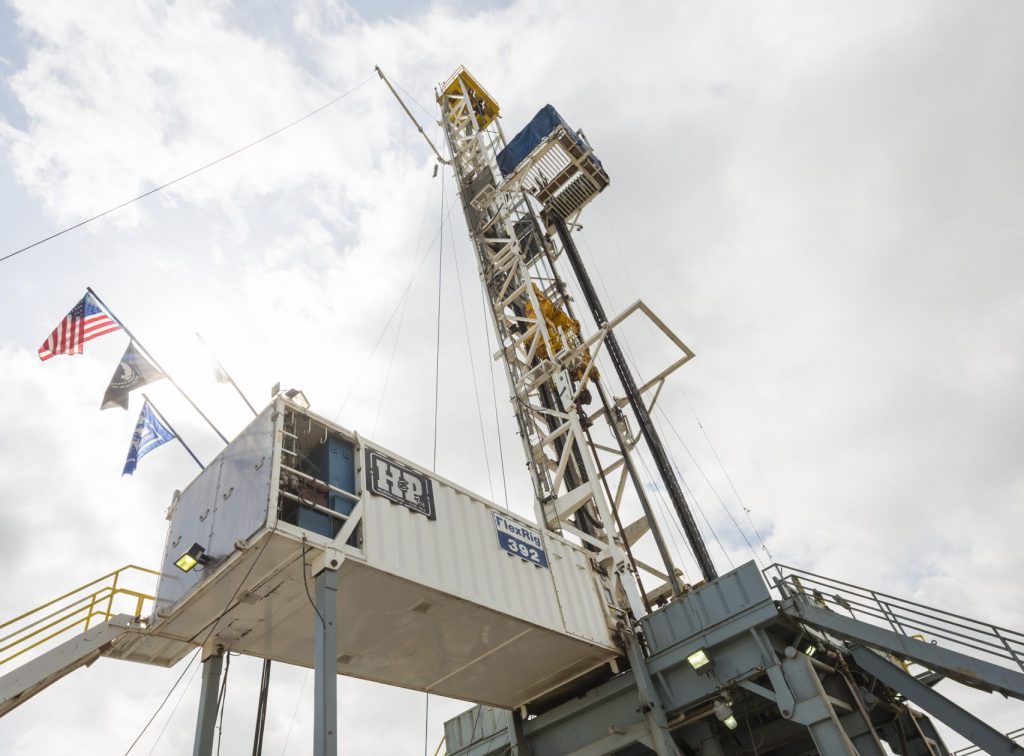
Helmerich & Payne rigs on the job.
Safety In Context
Both agreed that safety is important—that they will never do anything that knowingly jeopardizes anyone’s safety. But they pushed back at the mantra of “Safety First,” saying, in Mosvold’s words, “If safety was first, you’d stay at home—you wouldn’t even go out.”
Instead for them it’s “Safety while working.” Mosvold pointed out, “If there’s ever a conflict between safety and work, safety wins. We believe we can do it safely and, as an industry, we’ve proven that.”
A key part of safety is keeping speed in perspective, relying on the aforementioned logistics and preventive maintenance while maintaining all rig site safety procedures.
Said Mosvold, “We’re not only coworkers—we’re part of a family. I watched Sam have all his kids, all five of them. I’ve deer-hunted side by side with his kids. And that goes for a whole lot of different employees.”
Drill, Baby, Drill?
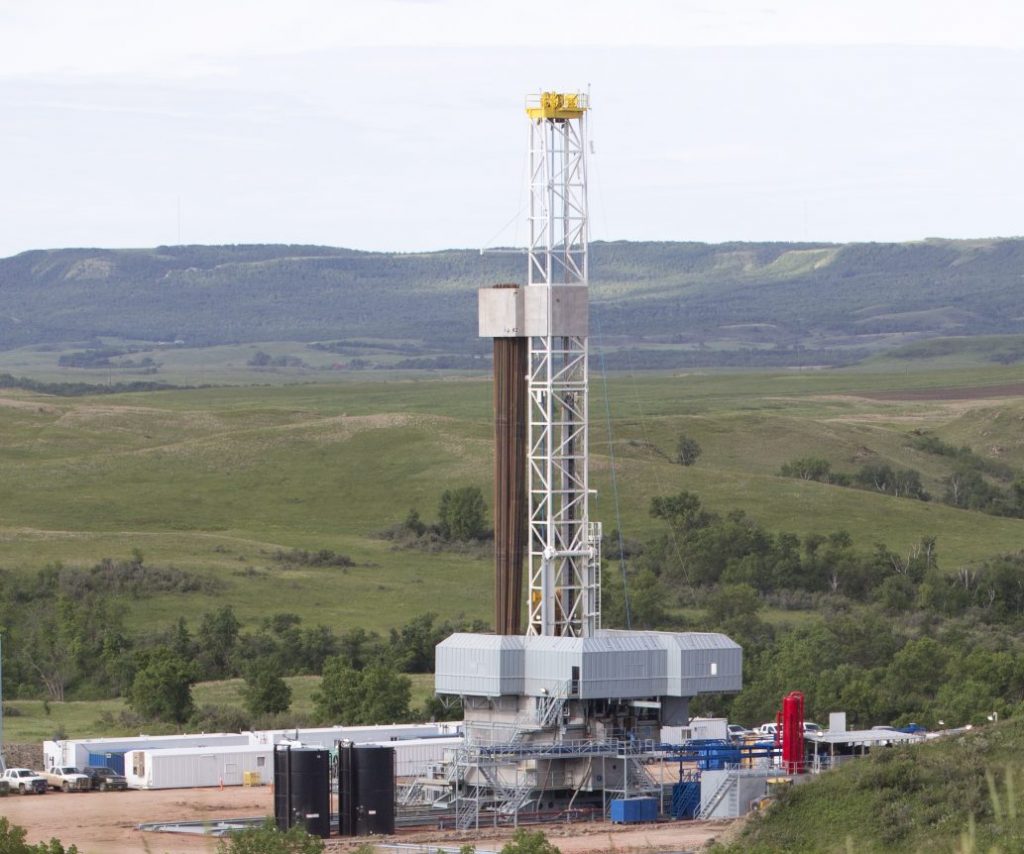
A Helmerich & Payne drill rig does duty in the Bakken.
If anyone in the oil industry was enamored with “drill, baby, drill” it would logically be a drilling rig company. The phrase, credited to former Maryland Lieutenant Governor Michael Steele at the 2008 Republican National Convention—and repeated there by former New York Mayor Rudy Giuliani and Alaska Governor/Republican Vice Presidential nominee Sara Palin, was Donald Trump’s campaign mantra.
But, said Hardin, “We do know realistically that if you look at overall market, the market’s going to speak, the market’s going to determine if we make that work.” He does see great benefit to a Trump presidency, however. “I do think that we’re going into a lot more friendly environment to the oil and gas industry, and that’s going to include downstream, midstream, and upstream,” particularly in the category of reduced regulatory stress.
EPA rules are not the only regulatory considerations on the list. “OSHA has clearly been weaponized,” said Mosvold, referring to increasing fines and enforcement of “completely ridiculous” overtime rules, and what he called its practice of only applying fines, not acting in an advisory capacity at all.
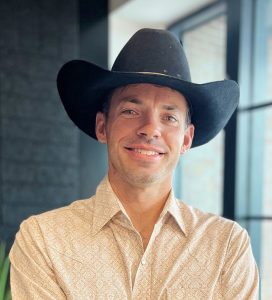
JT Brady
For Helmerich & Payne (H&P), meeting the challenge of long-lateral issues involves high-grading the entire rig, said J.T. Brady, senior manager of H&P’s Flex Rig Support Department. Of the many issues that involves, two of the most significant involve higher torque top drives, and then higher torque drill pipe to handle that. Every additional foot drilled involves more resistance, which means the top drive must push harder, and the pipe must handle that stress.
“We’ve upgraded that, and, in a similar way, we’ve upgraded our mud systems,” Brady said. Higher pressure mud systems actually made the upgrade from 5000 lb. psi to 7500 psi, which became standard around 2012-2015, he said. The mud part was easy, he related, because it involved only upgrading the fluid, not the pumps, gears, and motors. That change, he said, happened pretty quickly.
Plus, the arrival of multi pad drilling gave rise to the walking rigs mentioned above, in which one rig basically moves itself to the next stop, as long as it’s on the same location.
Rig Power Gets Charged Up
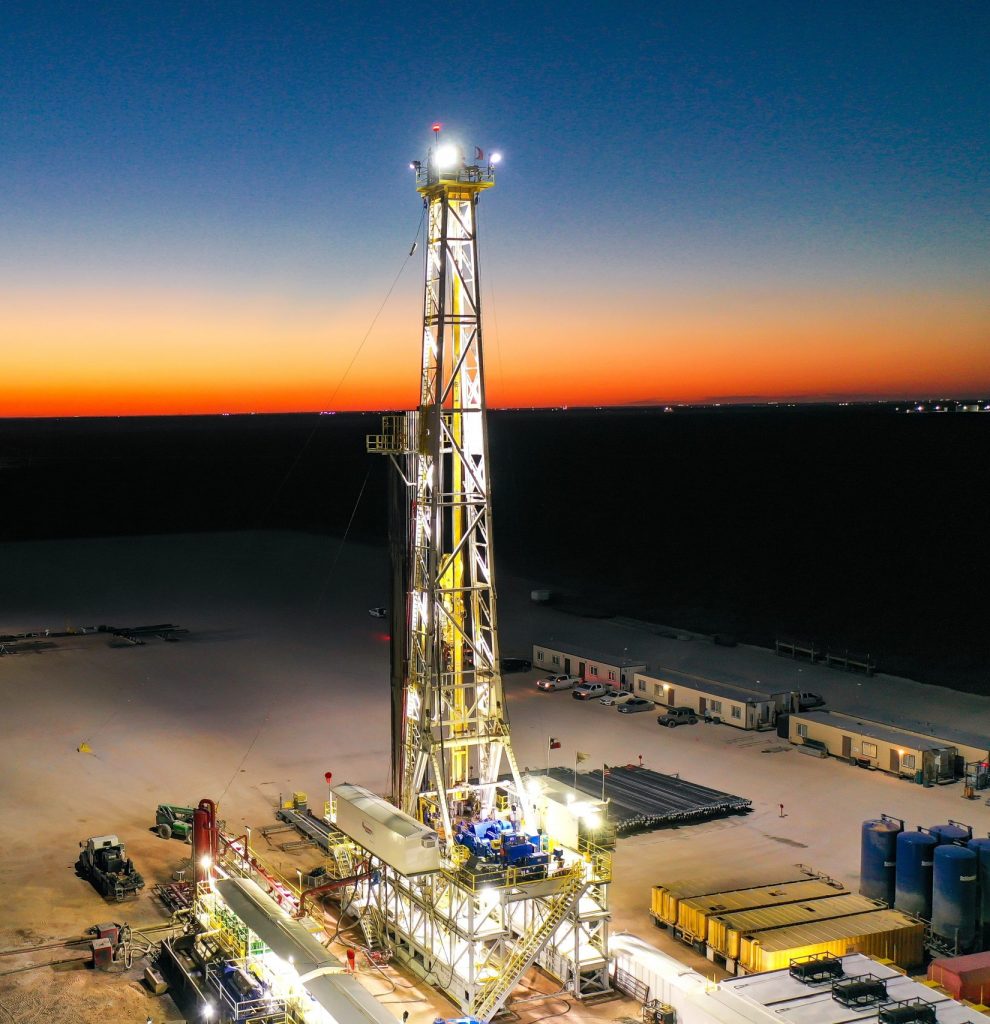
Scandrill rig
A combination of concerns including cost and greenhouse gas (GHG) emissions have driven H&P to move toward different power sources for those rigs. Two have emerged as leaders: using electricity from the grid when possible; and, when that’s not available, using engines that either reduce diesel use by incorporating natural gas, or that use exclusively natural gas.
Because it involves connecting to wires, the grid option is the preferred choice because it involves no on-site refueling. But it’s not always available. An industrial-strength grid extension to remote oil and gas locations sometimes takes months. As Brady pointed out, “If it was an easy problem [to solve], you’d see nearly the entire fleet on it.”
On a drill site with multiple wells planned, sometimes the grid reaches the location on well four or five, he noted, which is still a good thing. That’s when it starts saving diesel fuel costs and emissions, as well as Scope 3 emissions, which involve GHGs from fuel delivery trucks traveling to and from the site.
Reducing Costs and Emissions with Dynamic Gas Blending
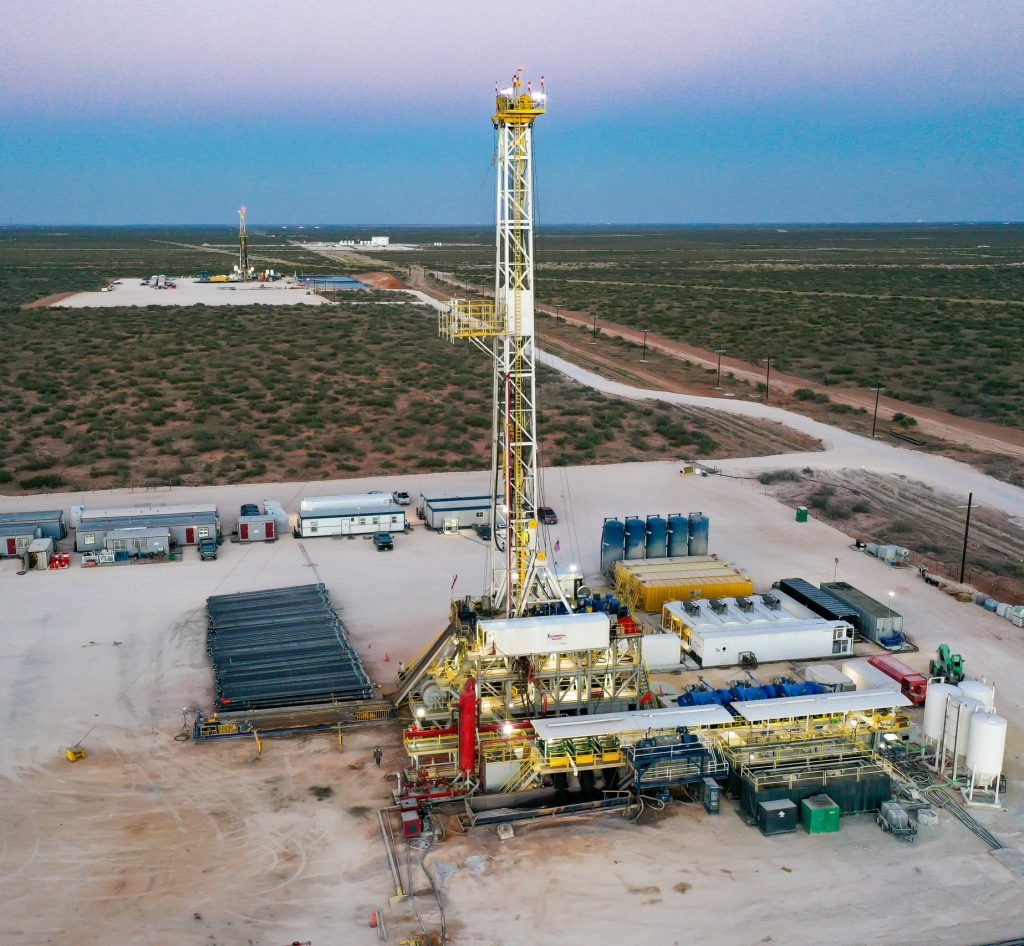
Scandrill rig
Mixing natural gas with diesel to reduce costs and GHG emissions has been around as a concept for about 20 years. But older systems that blended natural gas with the intake air had two main drawbacks, Brady indicated. They were limited in the amount of gas they could inject, and some of that gas didn’t burn at all—a situation known as “methane slip,” which in itself is a significant source of GHGs.
That option, known as a fumigated system, only replaced about 35 percent of the diesel with natural gas—better than nothing, but only one step in the right direction.
For the better part of two years, said Brady, Caterpillar (who makes the engines) and H&P have been working on what Cat calls a Dynamic Gas Blending Generation II (DGB Gen II) process that blends the two fuels at the port injection point, using a “more sophisticated operating system on the engine, that puts just the right amount of gas that can actually be burned into the system. So it has virtually no methane slip,” he said. Further, it replaces up to 75 percent of the diesel. It also reduces emissions by about 10 percent compared to using diesel alone.
Brady said DGB was borrowed from Caterpillar’s existing dual-fuel Tier 4 engines used across the industry. “They took the injection side of the engine and designed a way to retrofit that onto the engines that we use.” The ability to retrofit existing engines was a great cost benefit.
The first in-field test began in February of 2024, Brady noted, and they expect that by the time this article runs to have several in the field.
You Know the Drill
Longer, faster, more accurate—and greener and safer. Today’s drillers use advanced technology to meet ever-increasing and sometimes conflicting demands. H&P and Scandrill are helping the industry get where it needs to be.
A longtime contributor to PB Oil and Gas Magazine, Paul Wiseman is an energy industry freelance writer.
The post Rigging Up appeared first on Permian Basin Oil and Gas Magazine.
pboilandgasmagazine.com (Article Sourced Website)
#Rigging